adidas sport eyewear – Zu Besuch bei Adidas in Linz
In Linz befindet sich die Zentrale und die Produktion von Adidas Sport Eyewear. Angeblich würden dort alle Adidas Sportbrillen vor Ort produziert! Von der Sonnebrille bis zur funktionellen Sportbrille für den Downhill- oder Enduroeinsatz. Wir wollten uns selber ein Bild machen und statteten den heiligen Hallen einen Besuch ab.
Mal ganz ehrlich: bist du zu 100% davon überzeugt, dass eine Adidas Sport Brille in Österreichischer Handarbeit entsteht? Oder würdest du eher davon ausgehen, dass die Einzelteile in Containern aus Fernost angeliefert, in Österreich schnell zusammengebaut und dann mit dem Label „made in Austria“ verpackt und in den Handel geschickt werden? Also wir waren ja ehrlichgesagt vor unserem Besuch bei Silhouette, dem Hersteller von Adidas Brillen, ziemlich skeptisch. Wir sollten heute eines Besseren belehrt werden.
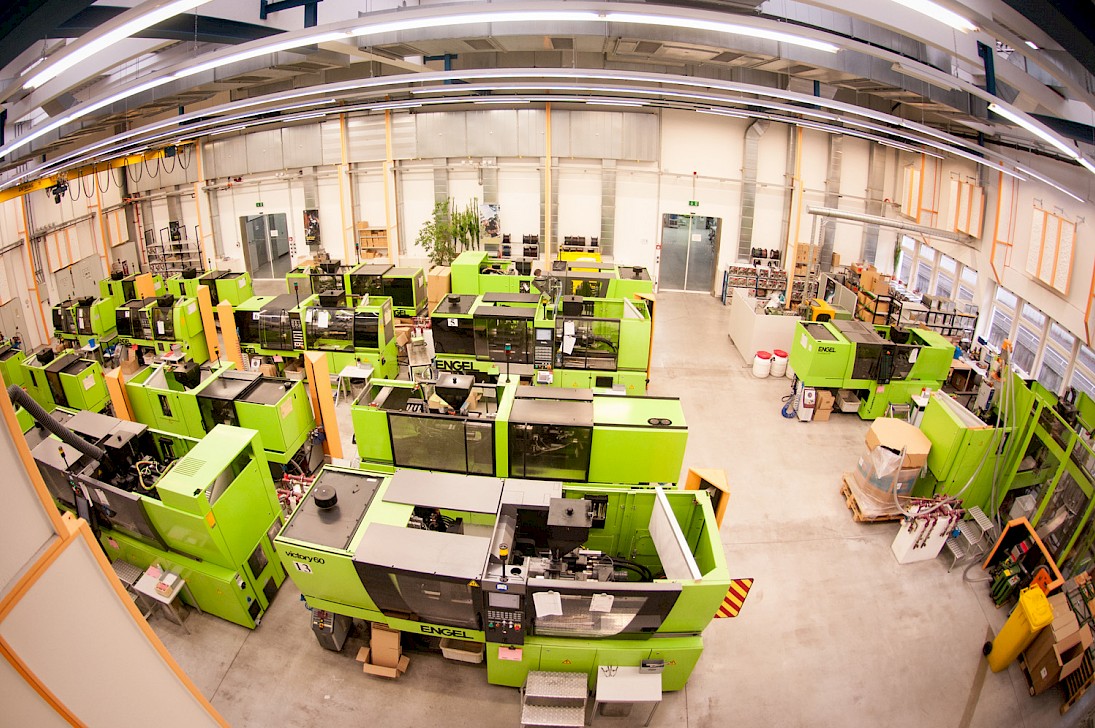
Riesige Halle, riesige Maschinen! Aus diesen grünen Spritzguss-Ungetümen fallen die meisten Einzelteile der Adidas Brillen heraus!
Silhouette ist ein echtes Traditionsunternehmen, 1964 gegründet und seither bis heute in Familienbesitz. Neben der Eigenmarke und einer neuen Fashion-Brand namens Neubau, stellt Silhouette als exklusiver Lizenznehmer alle Sport Brillen von Adidas her. Und zwar hier in Linz, im Headquarter der Firma mit rund 800 Mitarbeitern. Christian Jany nimmt uns in Empfang und kündigt schonmal an, dass wir nun den Werdegang einer neuen Adidas „Evil Eye Evo“, der Neuauflage der altebekannten „Evil Eye“, vom Granulat bis zur Verpackung quasi live verfolgen können. Was genau das bedeutet, davon haben wir zum jetzigen Zeitpunkt nicht den Hauch einer Ahnung.
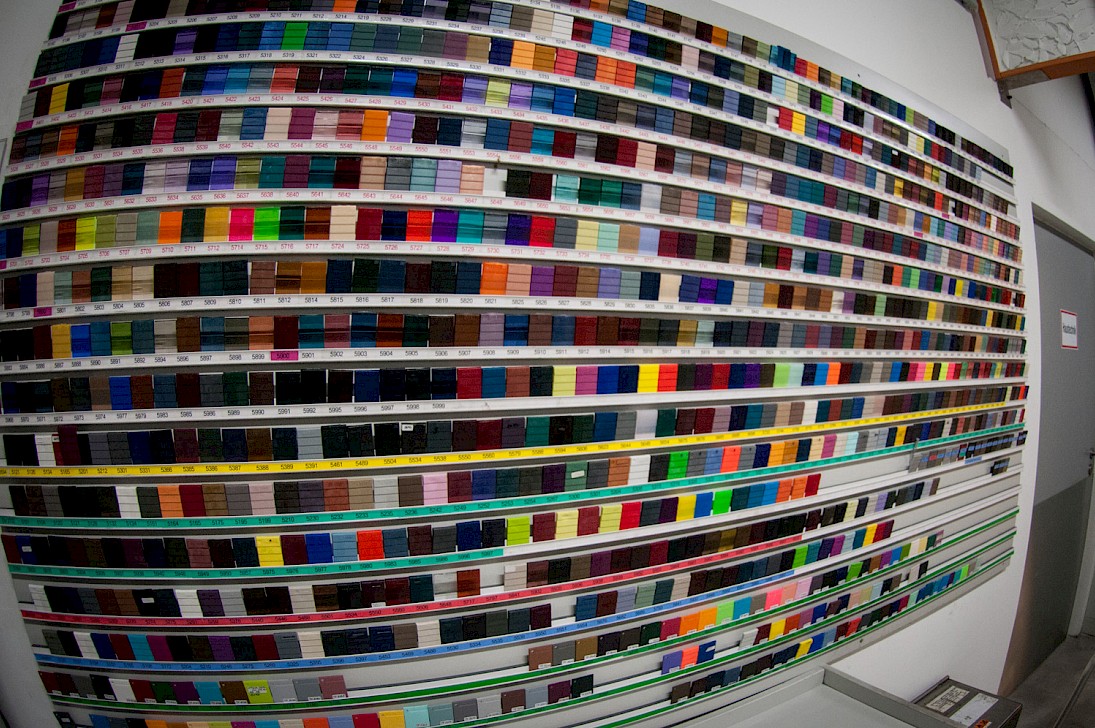
„kleine“ Farbauswahl: der Computer kennt zum Glück jedes einzelne Farbrezept...
Zu Beginn unserer Führung erwartet uns eine Schätzfrage. Christian will wissen, wie viele Arbeitsschritte unserer Meinung nach in einer „Evil Eye“ Brille stecken. Wir grübeln und rechnen ein wenig und kommen auf 20 Arbeitsschritte. Mit einer kleinen Reserve. Und wir staunen nicht schlecht, als wir die tatsächliche Anzahl erfahren: knapp 250 Arbeitsschritte stecken in jeder einzelnen Brille! Und jeder davon wird hier im Werk durchgeführt. Bevor eine Brille in Produktion geht, steht natürlich das Design an. Daraus werden dann 3-D Prototypen gefertigt, die unter anderem von den Adidas Athleten getestet werden. Wenn alle happy sind, kann die Produktion starten. Dafür müssen zunächst die nötigen Maschinen gebaut werden und selbst das passiert hier in Linz, im eigenen Werkzeugbau. Dort entstehen unter anderem die Formen für den Spritzguss, der ersten Station unserer Werksbesichtigung.

„Weichteile“, wie z.B. diese Anti-Rutsch-Pads im Brillenbügel, werden ebenfalls im Spritzguss-Verfahren aufgetragen
Im Spritzguss wird ein spezielles Kunststoffgranulat, das bei Adidas auf den Namen „SPX“ hört („X“ soll dabei für eine geheime Komponente stehen), bei rund 250 Grad eingeschmolzen. Soll das Teil am Ende farbig sein, werden sogenannte „Master Patches“, also farbige Granulatstücke beigemengt, ein Computer kennt dafür die genauen Rezepturen. Diese eingeschmolzene Masse wird dann unter hohem Druck in eine Form gespritzt, was dem Verfahren seinen Namen gibt. Nach kurzem Erkalten fällt dann der fertige Rohling heraus, der natürlich noch sehr „rau“ und scharfkantig ist. Auf diese Weise entstehen z.B. die Brillenrahmen, die Bügel oder alle Kunststoff-Kleinteile, die in so einer Brille verbaut sind. Nach demselben Verfahren werden aber auch z.b. im Brillenbügel integrierte Weichteile in die fertigen Bügel gespritzt und sind dann unzertrennlich damit verbunden. „Würde man diese Teile kleben, könnte es passieren, dass sie sich lösen“, weiss Christian den hohen Aufwand zu rechtfertigen.
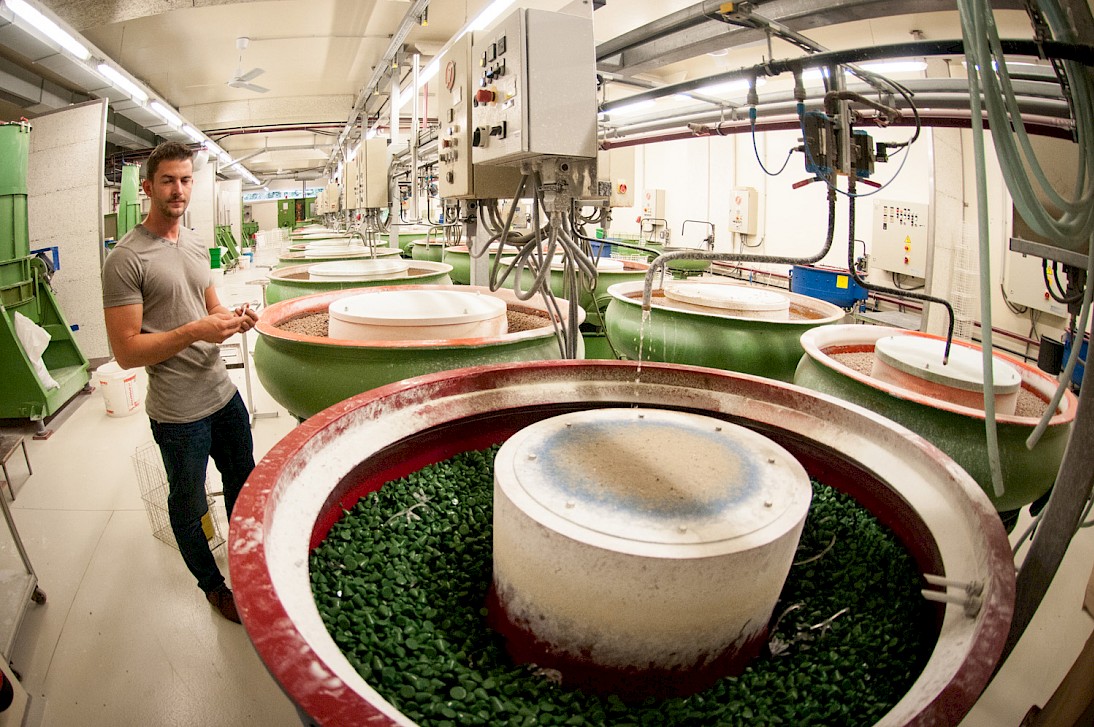
Die grünen Keramik Schleifkörper „scheuern“ solange an den Kunststoff-Rohlingen, bis diese ihr endgültiges, aalglattes Finisch erreicht haben
Um die scharfkantigen Rohlinge zu glätten und zu polieren, kommen sie in die „Scheuerei“. Dort befinden sich in riesigen Wannen unzählige Keramik-Schleifkörper, die durch ein Rührwerk ständig in Bewegung sind und so in einem zeitaufwändigen Prozess die hinzugefügten Brillenteile polieren. In bis zu 4 Scheuergängen, die jeweils 5-10 Stunden dauern, bekommen so die Kunststoffteile ihr endgültiges Erscheinungsbild. In der Scheuerei ist es wirklich laut, so dass wir einen Gehörschutz tragen müssen. Das hier ist echt technisch, richtige Industrie, hier passiert etwas, das kann man sehen, hören und riechen!
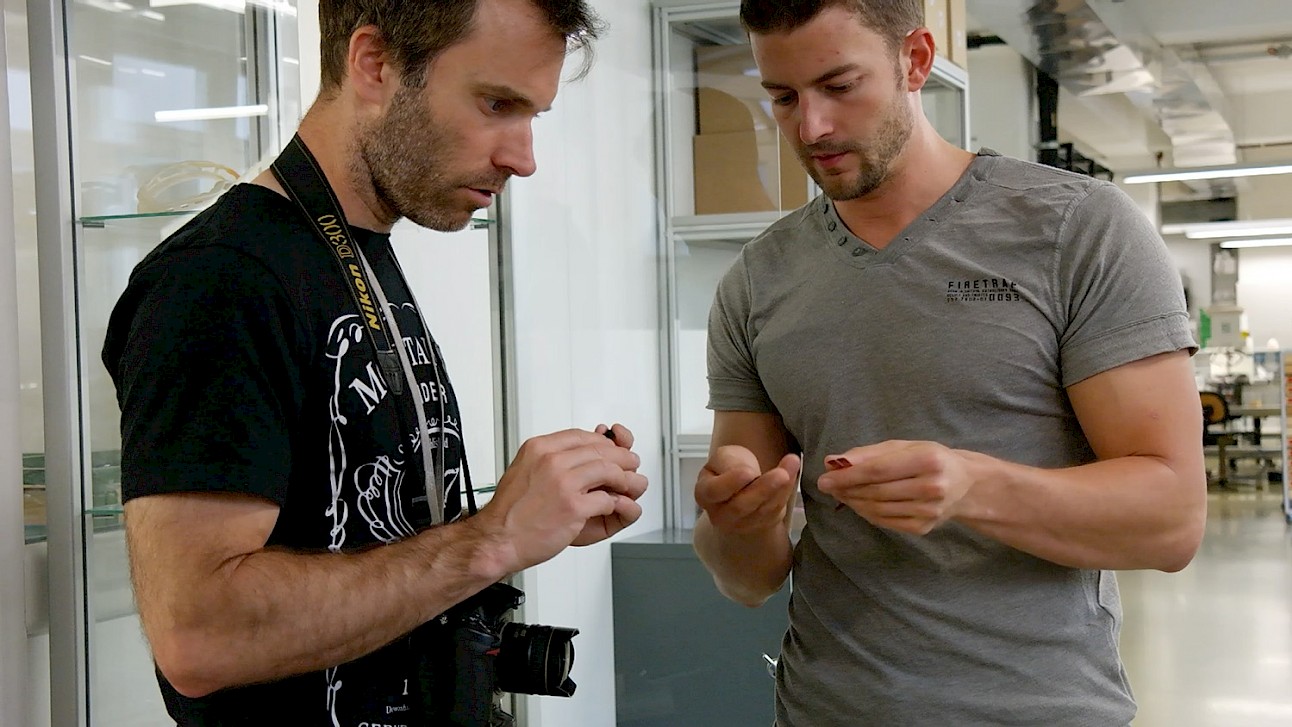
Nächster wichtiger Stopp: die Druckerei. Diese hat aber so gar nichts mit normalem Druck auf Papier zu tun. Denn stellt euch vor: es werden ja gebogene, runde oder eckige Teile bedruckt. Keines davon hat eine ebene Fläche, daher ist es sehr kompliziert, diese Teile sauber zu bedrucken. Umgesetzt wird das mit einer Art 3-D-Stempel. Die sehen teilweise aus, wie eine übergroße Kartoffel und werden, nachdem sie mit dem genauen Farbmuster vorbereitet wurden, mit definiertem Druck auf das zu bedruckende Teil „gestempelt“. Die Einrichtung einer solchen Druckmaschine kostet viel Zeit und Erfahrung, wovon wir uns direkt nebenan überzeugen können, denn hier legt gerade der Druckereichef selber Hand an. Mit gekonnten Handgriffen justiert er die Maschine millimetergenau und überprüft das Ergebnis penibelst.
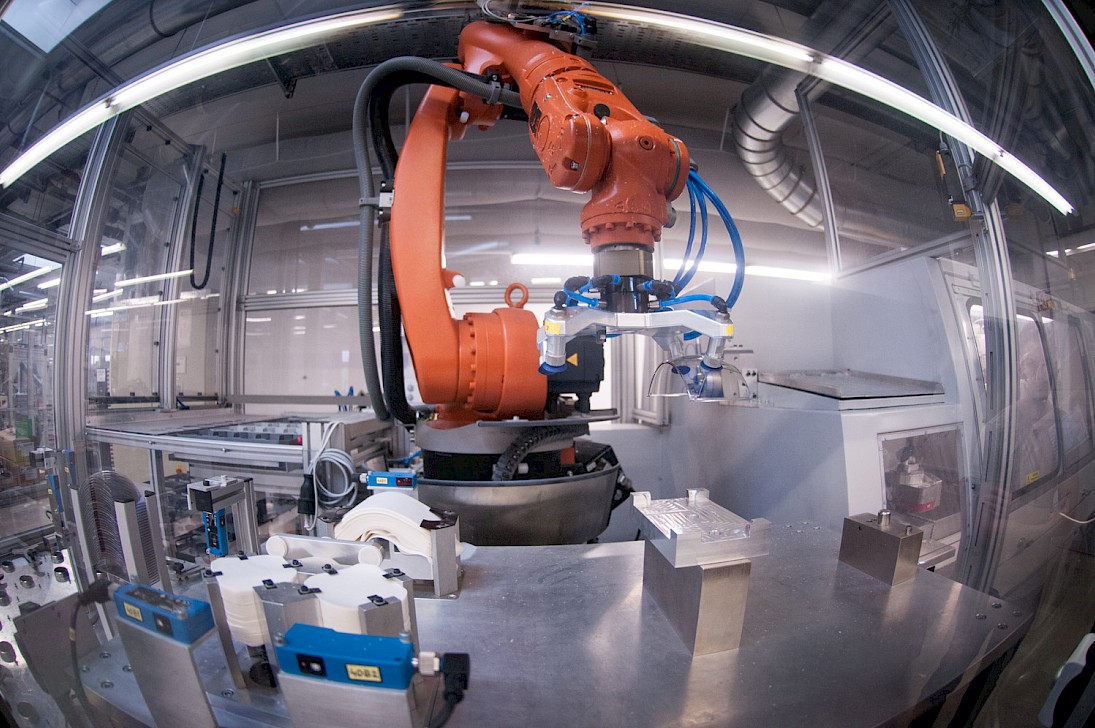
Vollautomatisch - dieser Robotor ist einer der zuverlässigsten Mitarbeiter im Werk und zuständig für das Fräsen der Brillengläser
Was noch fehlt, sind die Brillengläser, oder auch „Filter“, wie der Fachmann sagt. Auch diese werden hier in Linz in Form gebracht. Vollautomatisch von einem großen Roboter, der Filter für Filter aus einem großen Magazin entnimmt, die Form ausfräst, ggf. Bohrungen hinzufügt und sie dann am Ende des Prozesses ordentlich stapelt.
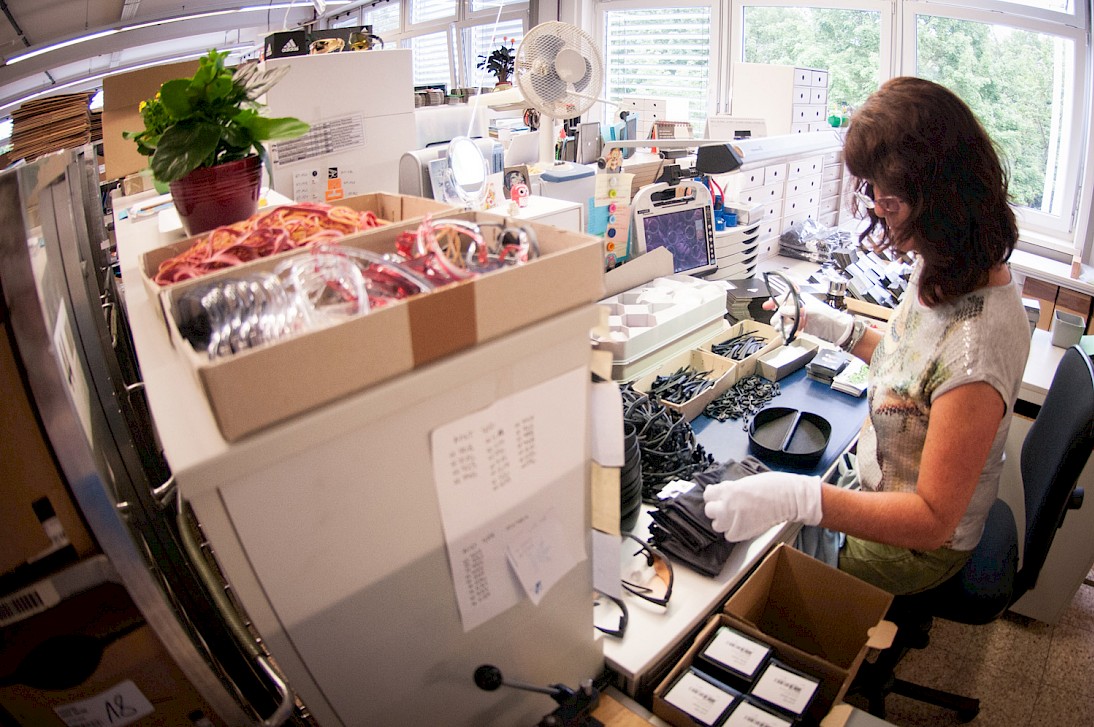
Die Endmontage wird bei Adidas ebenfalls per Hand durchgeführt. Inklusive individuellem Qualitäts-Check
Nun geht es ans Zusammenbauen und Verpacken. Dabei wird jede Brille gecheckt und verlässt nur das Werk, wenn alles einwandfrei ist. Ganz ehrlich: nachdem wir das gesehen haben, haben wir keine Fragen mehr, warum eine Adidas Brille nicht ganz günstig ist. Wir konnten uns selbst davon überzeugen: es ist nicht nur ein Spruch, jede Brille ist tatsächlich „made in Austria“. Zum krönenden Abschluss unseres Besuchs bekommen wir noch die nagelneue „Evil Eye Evo“ ausgehändigt, die wir nun selber testen können und euch im Folgenden im Detail vorstellen.

Fotos: Martin Donat
Gepostet am 28.10.2016 von Martin Donat |